Polymer-derived ceramics with graded structures for phase separation and catalysis
The functional element in devices for phase separation (liquid-gaseous, gaseous-liquid) is a porous structure. Nowadays, metallic meshes are used to provide phase separation. Since metallic meshes exhibit several disadvantages like limitations in geometry and problems in the connection to the supporting structure, there is a need of porous structures which combine the functionality of phase separation with near-net-shaping processes. Furthermore, precisely designed gradients in the pore structure are supposed to improve the performance of phase separation devices. Near-net-shaping of ceramic parts is widely investigated and among the great variety to produce porosity in ceramics, freeze-casting is a templating method which allows for highly flexible designing the pore structure at the same time. Solvent crystals act as templates to form open porosity after drying and sintering. Properties such as pore morphology, pore size and open porosity can be adjusted in a wide range by adapting process parameters such as the solvent, the freezing front velocity and solid loading. In this project the freeze casting process of preceramic polymers should be used to produce porous monoliths with gradients in porosity, pore size and pore morphology. In preliminary works we already elaborated the fundamental knowledge to prepare PDC monoliths by freeze-casting using different solvents (P02/01), P02/02). In order to obtain gradients, controlling the solidification conditions like freezing front velocity and freezing direction is crucial. Furthermore, freezing in multiple steps offers the possibility to further increase the complexity of gradients in the pore structure. Additionally, near-net-shaping of complex shapes should be achieved by adapting the casting molds as well as the freezing process. Using preceramic polymers as starting material allows for the adjustment of the hydrophilicity/hydrophobicity of the structure. The development of the freeze cast structures for phase separation experiments will be performed in cooperation with project P10/03. Here the modelling of the setting behavior and of the capillary transport as well as the experimental measurements of the phase separation will be conducted. For interpretation and modelling µCT-data will be used (P04/03, P09/03). Besides being the active element in phase separation devices, gradient structures are of great interest for a variety of applications. Gradients in pore structure are essential to improve mass transport and thermal transport properties of monolithic catalysts. Further potential applications are filtration, emulsification (P18/02, P07/03) and as electrode materials for Microbial fuel cells (P15/02, P16/02).
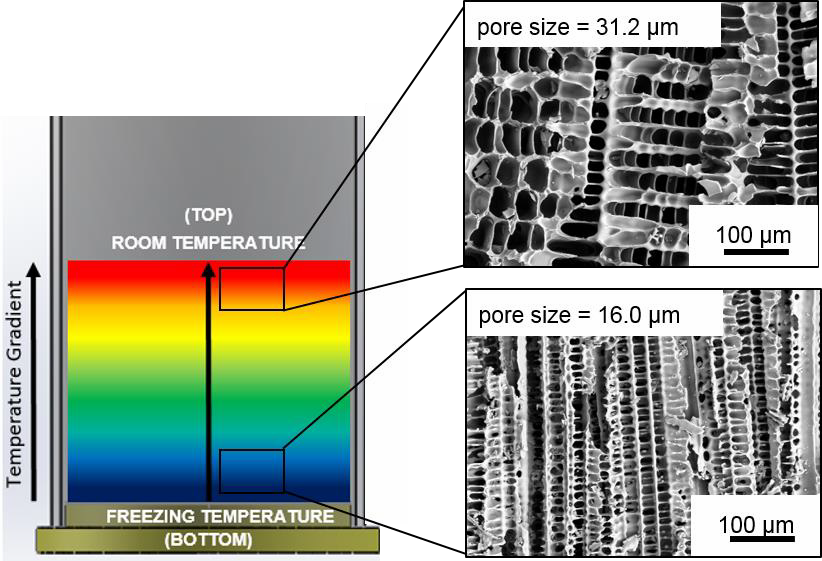
Contact: Wilhelm, da Rosa Braun
Publications within MIMEMIMA:
D. Schumacher, M. Wilhelm, K. Rezwan (2018), Modified solution based freeze casting process of polysiloxanes to adjust pore morphology and surface functions of SiOC monoliths, Materials and Design, Volume 160, 1295-1304, https://doi.org/10.1016/j.matdes.2018.10.048
H. X. Zhang, C. Fidelis, A. L. Serva, M. Wilhelm, K. Rezwan: Water-based freeze casting: Adjusting hydrophobic polymethylsiloxane for obtaining hierarchically ordered porous SiOC, Journal of the American Ceramic Society, 2017, pages 1-12, http://dx.doi.org/10.1111/jace.14782.
H. X. Zhang, C. Fidelis, M. Wilhelm, Z. Xie, K. Rezwan: Macro/mesoporous SiOC ceramics of anisotropic structure for cryogenic engineering, Materials and Design,2017, Volume 134, pages 207-217, http://dx.doi.org/10.1016/j.matdes.2017.08.039.
H.X. Zhang, P. D’Angelo Nunes, M. Wilhelm, K. Rezwan: Hierarchically ordered micro/meso/macroporous polymer-derived ceramic monoliths fabricated by freeze-casting, Journal of the European Ceramic Society, 2016, Volume 36m, Issue 1, pages 51-58, http://dx.doi.org/10.1016/j.jeurceramsoc.2015.09.018.
Y. Grebenyuk, H. X. Zhang, M. Wilhelm, K. Rezwan, M. Dreyer: Wicking into porous polymer-derived ceramic monoliths fabricated by freeze-casting, Journal of the European Ceramic Society, Volume 37, Issue 5, May 2017, pages 1993-2000, http://dx.doi.org/10.1016/j.jeurceramsoc.2016.11.049.