Simulation of structural changes of mesoporous films and layers during liquid infiltration and drying
Highly porous nanoparticle films and layers with defined mesoporosity are essential in many applications including catalysis, energy storage and gas sensing. Our group has made several contributions in these fields using direct nanoparticle deposition from the aerosol phase or from a printing technology of nanoparticles that allow for dry, solvent free deposition of such microporous films. Some applications, however, require liquid infiltration (imbibition) and even drying of such porous structures during their applications including electrochemical characterizations, polymer hybrid materials and liquid electrolyte cells. It has been observed that the microporous structure and the pore size distribution can be significantly altered during such process steps. In the past years, we have obtained and published experimental evidence of such changes with respect to structural properties of the porous layers as well as surface tension, wetting angle and viscosity of the fluid. While hypotheses of the structural changes during imbibition and drying have been proposed (Figure 1) a mechanistic understanding is still lacking. A discrete element method (DEM)-computational fluid dynamics (CFD) coupling method will be used to include capillary effects. A model will be developed that takes fluid flow during imbibition and drying with respect to the acting forces on the microporous structure into account. These forces act on the structure itself leading to rearrangements by breaking and forming old and new weak particle bonds, respectively. The porous structure itself will be generated with Monte Carlo simulation and DEM, depending on the degree of compaction before the imbibition / drying takes place (e.g. large compaction in case of battery structures). It should be noted that three phases have to be considered in this model / simulation scheme and that a conscious remeshing is required. For a technical realization, a coupling of LIGGGHTS (an open source discrete element method particle simulation software) and OpenFOAM (an open source computational fluid dynamics toolbox) as well as in-house codes for layer preparation and compaction (all open access) will be done. The simulations can then be realized with a parallel simulation scheme. Such a model approach can be validated with our available experimental data (with P05/02, P04/03, P05/03, P10/03).
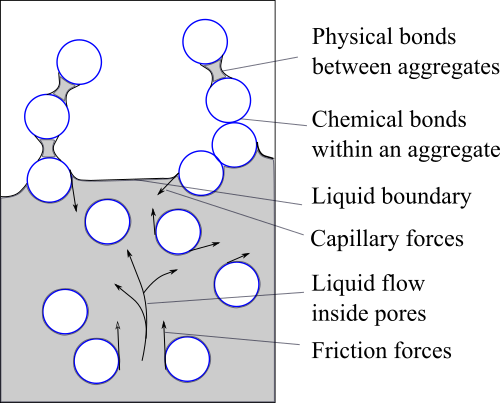
Contact: Mädler, Wriedt, Baune